The use of vitreous enamelling dates back to Egyptian times, around 5000 years ago. An art that was perfected by the Russian goldsmith/jeweller Carl Faberge around the end of the 19th century. Today, the process of decorating precious metals with vitreous enamels is undertaken in exactly the same way.
It is a long and intensive process which takes years to perfect. It is therefore no surprise that there are only a few experienced enamellers who can decorate precious metals in this way.
Onoto are proud of the immaculate quality of craftsmanship and expertise that our goldsmiths produce in the production of our unique pen designs such as the Horatio Nelson, British Museum and Xu Zhimo Collections.
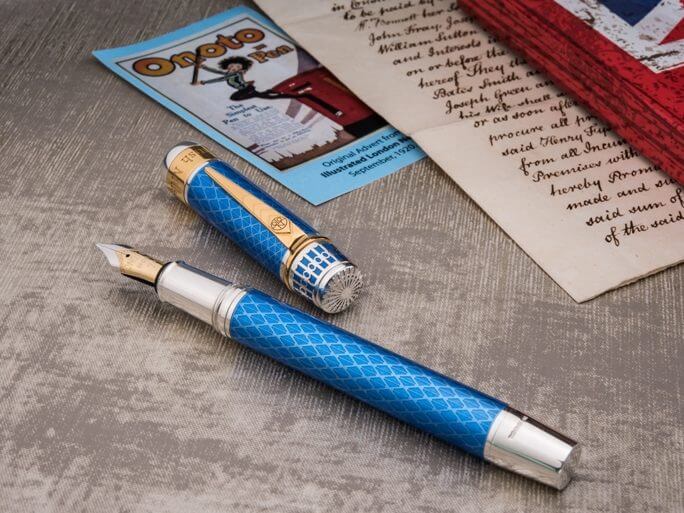
Onoto’s master goldsmith describes the processes he uses to decorate the Onoto range of enamelled pens:
“First, using a chemist’s mortar and pestle (a little larger than those you find in most kitchens), a mixture of silica, purified water and metal oxides is ground by hand. It takes several hours of painstaking grinding before the right consistency is achieved. The mixture is continuously rinsed through with purified water to take out any impurities. Only craftspeople with years of experience in working with this material know exactly when to stop grinding, as each colour “behaves” slightly differently, so shortens or lengthens the grinding time.
Now, here’s the part that seems totally out of place in this hi-tech age. Once the silica paste has reached the right consistency, goose quills (yes, goose quills!) are used to apply each coat of the enamel paste in the traditional manner. The quills come from a local farm and are carefully selected acc ording to the “fineness” of the enamel we are working with. The quill is sharpened, rather like a pencil, to a fine point so application of the enamel can be carefully and meticulously applied to the engraved surface of the sterling silver or gold pen. The application of enamel to the metal is a highly skilled craft, each enamelled component of the pen taking several hours to complete.
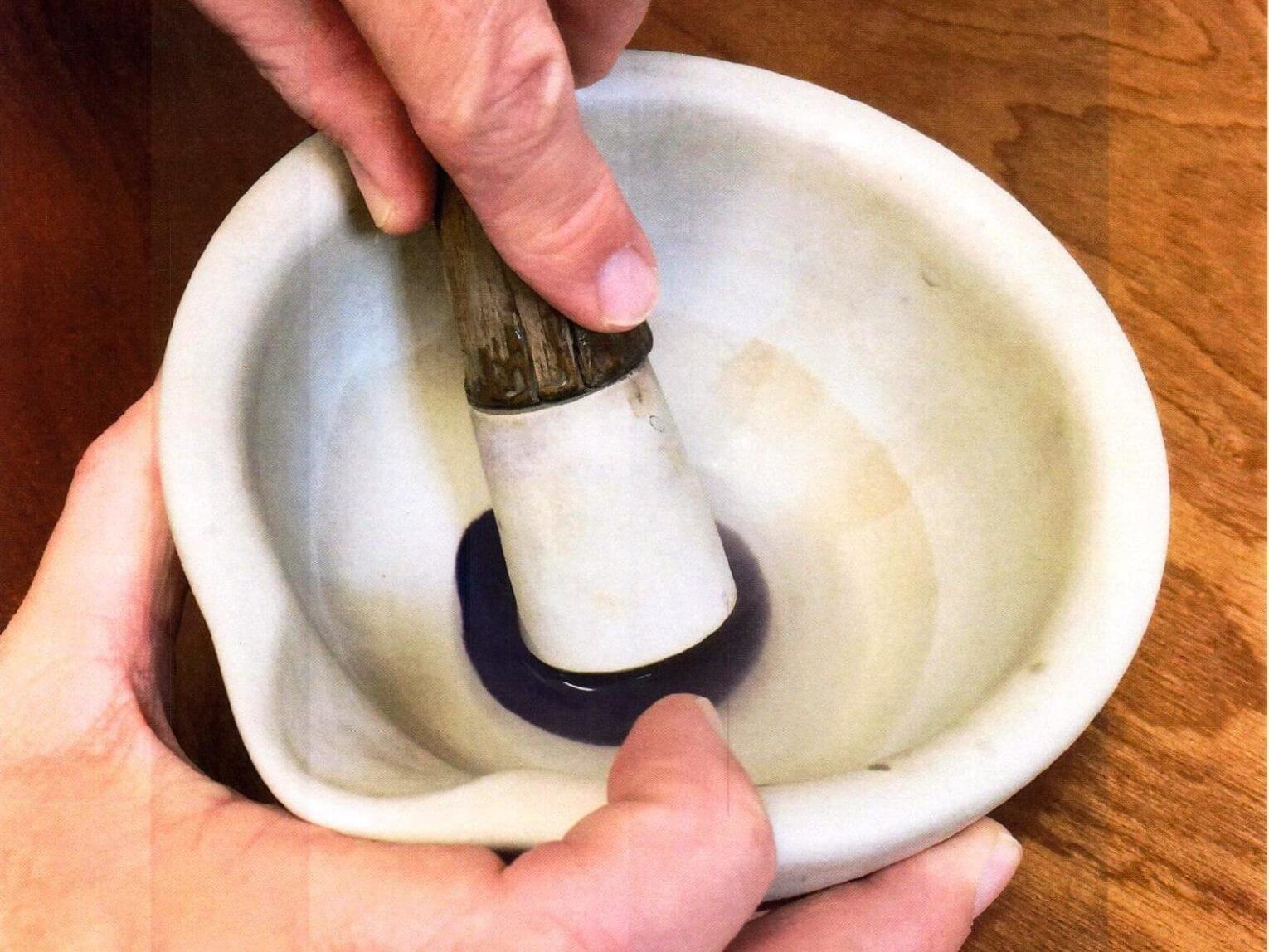
Why do we use goose quills?
Well, we have tried lots of other media but nothing gives the same combination of flexibility, precision and the ability to hold the enamel paste. Once a layer of enamel has been applied, each individual pen part is ‘fired’ in a furnace at temperatures between 750° and 850°C, depending on the colour of the enamel being fired. The temperature is critical. As the enamel paste heats up it starts to melt, becoming like liquid glass and fuses with the metal beneath it. Each firing may only take a few minutes, but it has to be watched very closely; too long and the metal (gold or silver) will start to melt; too short a time and the enamel will not ‘fuse’ to the metal.
After each firing, the pen parts are removed from the furnace and allowed to cool naturally before the next layer of enamel paste is applied. This process may involve 3 or 4 applications and firings, before the enamel shows the depth of colour and the translucency we require.

Once the enamel has been applied and fired satisfactorily, each enamelled pen part is individually ground with a diamond or carborundum file to smooth and shape the surface and ensure the enamel is of the correct depth to allow the guilloché (engraved pattern) on the metal underneath to show through.
Finally, the pen is buffed and polished to give maximum ‘show’ to the translucent enamel and the guilloché pattern.
As you might imagine, with a process that’s as technically challenging as this, and using completely natural materials, there has to be an extraordinary amount of painstaking examination at every stage. Of course, there are sometimes tiny spots or blemishes in the enamel – they are inevitable where natural materials are being used. We like to think of them as ‘signatures’ or birthmarks confirming the natural origins, uniqueness and character of each enamelled pen we produce.
The finished result is truly a work of art. There’s nothing mass-produced or mechanical about these pens, simply old-fashioned British craftsmanship, expertise and pride in the finished result.”
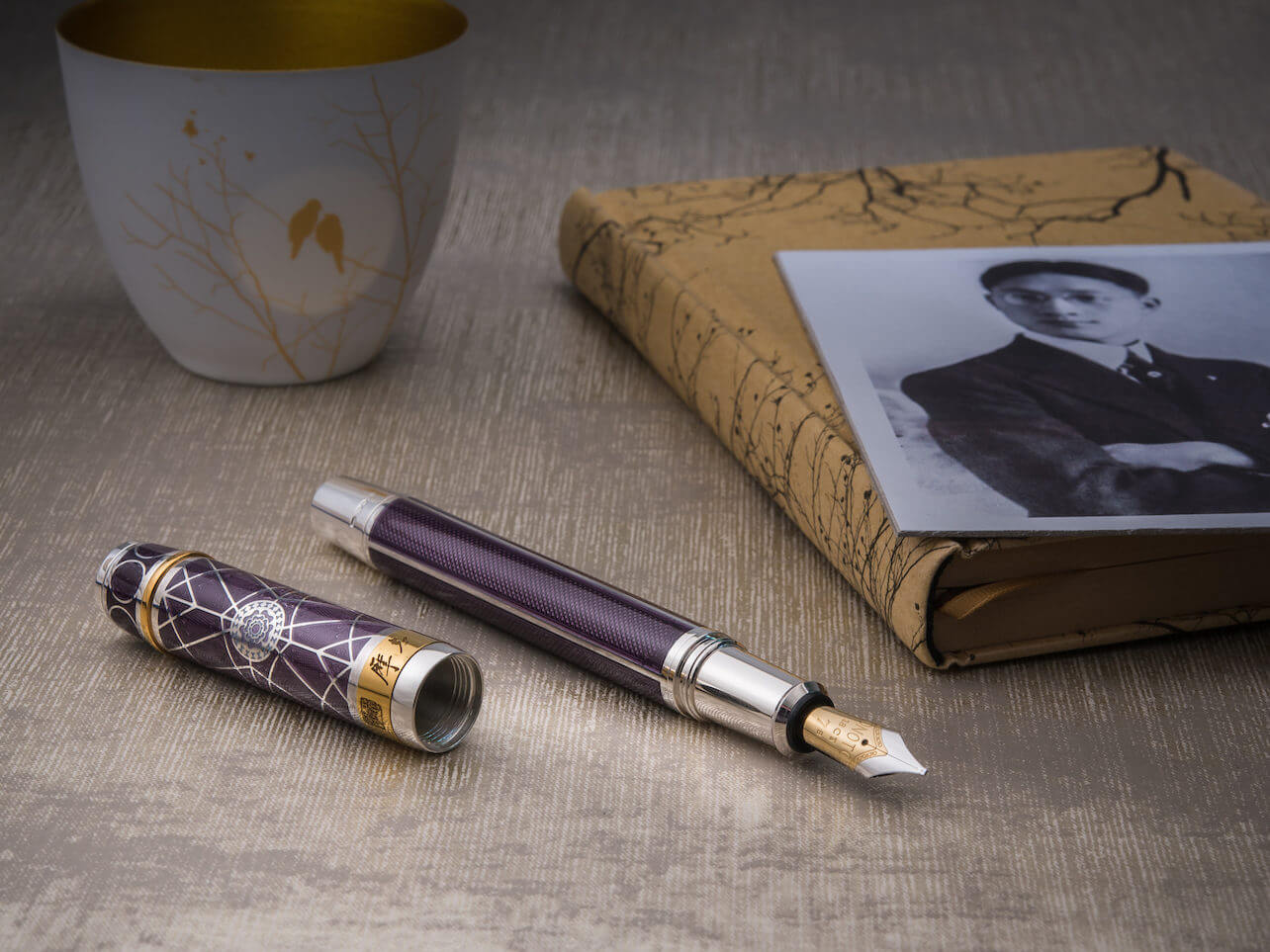
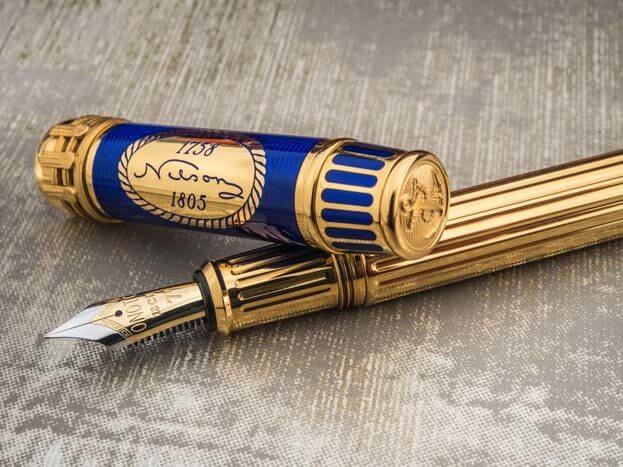
The enamelling process when applied to guilloché engraved sterling silver or gold creates a pen which bears all the hallmarks of true artistic and creative genius. As Fabergé discovered, the combination of translucent vitreous enamel and guilloché engraved sterling silver or gold is simply stunning!
A vitreous enamelled Onoto fountain pen is the epitome of the very highest British craftsmanship; tactile and sumptuous to hold; perfectly balanced; a prized possession that will be used with pride, and admired and cherished for generations to come.
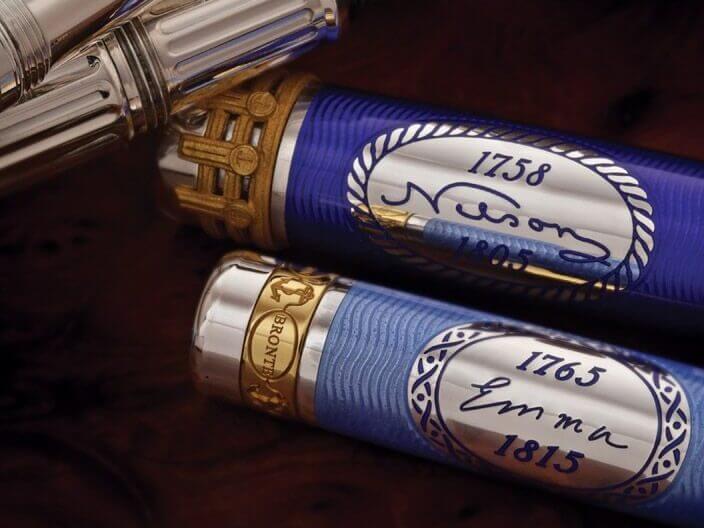
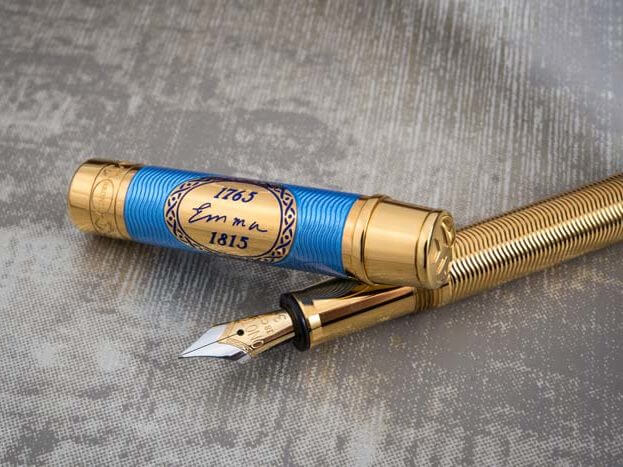